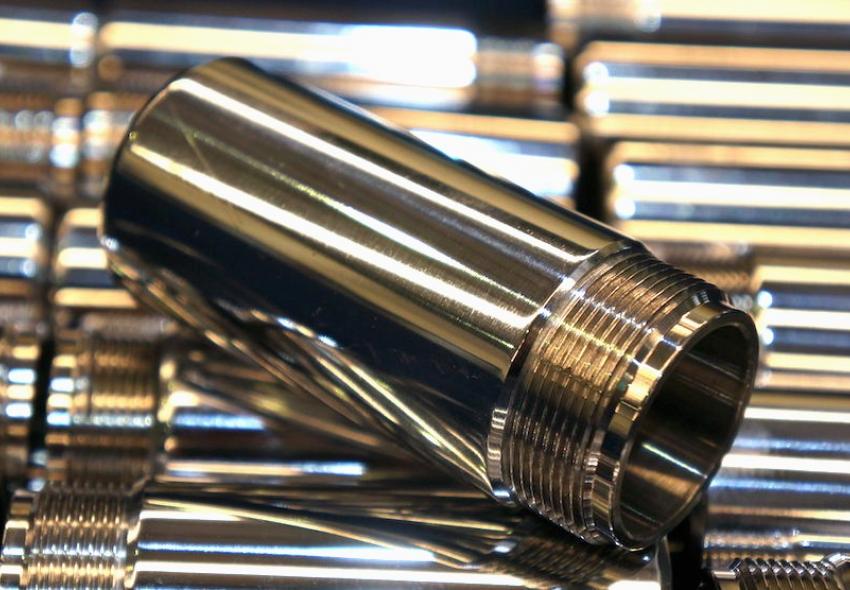
Types of Electroless Nickel Plating
In many instances, plating is applied with the aid of an electrical current. However, Electroless Nickel plating is used to deposit nickel without the use of an electric current. The coating is deposited by an autocatalytic chemical reduction of nickel ions. Electroless nickel comes in three different types. Low-Phosporous, Mid-Phosporous, and High Phosphorus baths are commercially used. Some baths will run other components in it, like silicon, Teflon, and boron to add other characteristics to the coating. Electroless nickel is a uniform deposit anywhere the solution meets the base material. Areas can be masked off if needed but can be challenging to make it watertight and adds cost.
Low Phosphorus Electroless Nickel
Developed in the 1980s. Deposits contain 2 to 4 percent phosphorus. The coatings offer improved hardness and wear characteristics, higher temperature resistance, improved solderability and increased corrosion resistance in alkaline environments. The baths typically are run at a lower temperature and higher pH than the other baths. The deposits are microcrystalline and possess high as – plated hardness of 60 HRC. This coating is used in applications requiring excellent wear resistance (without heat treatment).
Mid Phosphorous (Phos) Electroless Nickel
This contains 6 – 9 percent phosphorus. It is the most commercially used electroless nickel. The nickel deposits as a bright and semi-bright finish. Hardness can range from 42 – 47 HRC as deposited. The deposit can be heat treated at temperatures of 500° - 700° F to achieve deposits of 58 – 62 HRC. The deposit does lose corrosion resistance from this. Heat treatment or baking can also improve adhesion of the deposit.
High Phosphorous (Phos) Electroless Nickel
High phos electroless nickel offers the highest corrosion resistance of all the EN deposits. Very good for protection from highly corrosive acidic environments. The deposit is non-magnetic and is 42 – 45 HRC as deposited. The deposit can be heat treated at 500° - 700° F to achieve deposits of 58 – 62 HRC. The deposit loses some corrosion resistance but ends up close to mid phos EN corrosion resistance, but with extra hardness.
Deposits
A wide range of thickness can be put on. Ranging from .0001” thick to .008” thickness. Many times, the deposit even in .003” - .004” thickness can be plated to size with no grinding afterward. Areas can be masked off but usually, it is more cost-effective to plate the entire part.
Baking
Baking can improve hardness, adhesion and prevent hydrogen embrittlement. The temperature ranges and time vary depending on what is being accomplished. Inert gas ovens can keep the deposits from tarnishing during this operation if appearance matters. This is a more costly oven to use because of longer cycles from gas purging and cool down. ChromeTech has both types of ovens to service its customers. Contact us with any questions.
Contact us to explore whether low-phos, mid-phos, or high-phos may be the best coating/plating for your use.